Whether we are talking about industrial or home usage, the gratings offer a solutions for several problems.
We offer a wide range considering both the raw material and the technical content and most of our offer can be delivered straight from our warehouse, the rest based on the order to our partners.
Order simply from our webshop or ask for an individual quotation:
Usage areas of the gratings
building industry
canal and manhole covers, scaffolding supports, etc.
interior design
dividing walls, outdoor furniture, etc.
air conditioning
pavements for chimney sweepers, roof air conditioning, service pavements, etc.
food industry
walking surfaces, etc.
machine industry
walking surfaces, etc.
automotive industry
single steps, etc.
Basic information regarding the gratings
The gratings are flat reliefed grid-structures made from different raw materials, composed from bearing and transverse bars, which are suitable for sustaining loads. The load sustaining elements of the grids are always the bearing bars, which are made from suitably dimensioned steel strips (or other materials, e.g. stainless steel). The gratings sustain load only in one direction (the one of the bearing bars). This is why it is primordial to mark clearly the length of the bearing bars: always the dimension of the first given sheet side. In order to avoid the risk of accidents due to the interchange possibility of the sides it is advisable to avoid designing square grids.
In case this cannot be avoided then the suitable support of all the four sides is necessary.
Technical terms
The components and other basic concepts of the gratings may be summarized as follows:
1. Bearing bars: the load supporting element of the grid, steel strip placed on its edge, with a cross-section chosen according to the load demand.
2. Transverse bars: does not take part in supporting the load on the grid, it stiffens the bearing bars against turning and forms the grid picture together with them.
3. Dressing materials: do not take part in supporting the load, they are strip steel or steel sheets with special “U” or “T” profiles which close the bars' ends and border the grid sheets.
4. Gridding: the distance between the bearing and the transverse bars. Several grid dividing variations are possible. Choosing the grid dividing to be used increases the freedom of the static design. It makes it possible to synchronize and optimize the demand regarding the loading and the actual load supporting capacity. Of course, the grid dividing has an important influence on the specific price beyond the static point of view.
5. The grid picture may be defined randomly by varying the main and side grid directional division.
6. Light dimension (grid dimension) the free (light) area bordered by the main and the side ribs.
7. Bearing bar direction: the technical terms of "width" and "length" cannot be used in connection with the walking grids as these lead only to confusion and to products which cannot be incorporated. Instead the two terms are the bearing bar direction and the transverse bar direction. The bearing bar dimension which is the first one given from the dimensions of the grid sheet is measured from the support axis to the support axis, between the external surfaces of the bordering sheets perpendicular on the bearing bars.
8. Overhanging support (edge): on the lower area of the gratings there can be shaped one or more overhanging bordering sheets with increased height and sheet thickness. The aim is to bridge the different heights or the cost effectiveness.
9. Edge slat (ankle slat): edge frame on the upper surface of the edge slat overhanging on one or more sides, which stop objects from falling.
10. Grid framed by angular profile: such grid to which angular profile was welded on one or more sides turned outwards and downwards. At these grids the angular profile is the load supporting, the grid is placed on them onto the building.
Quality of the materials
The gratings are usually made out of hot and/or cold rolled unalloyed steel.
Besides the conventional steel raw materials the grids may be manufactured out of stainless steel or aluminium.
Protection against corrosion
The protection against corrosion of the steel grids is the hot dip galvanizing, which makes the products suitable for both outdoor and indoor use.
The hot dip galvanizing layer has to make up with the demands of the standard.
The pre-treated gratings are coated with a galvanized layer with a cleanliness of min. 98.5 %, which ensures that in case of normal mechanical stress (e.g. traffic, drive-through) the galvanized layer does not come off.
Loading capacity
The permissible loading of the gratings has to determined from standard DIN 24537, that of the steps and the spiral steps from standard DIN 24531, taking into account the useful loads prescribed by standard DIN 1055.
The named DIN standards satisfy the MSZ 15021/1 domestic standard on the load support of the high building structures, together with those of the domestic standard MSZ 15021/1, MSZ 15021/2 the rigidity of the high building structures as well.
Dimensional accuracy
The demands regarding the dimensional accuracy of the gratings and steps are stated in the standards DIN 24537, DIN 24531 and DIN 24530, in which further references can be found.
In the absence of the domestic regulations, the regulations and directives are summarized by the RAL- GZ 638 of the German Walking Grid Manufacturing Association on the shape accuracy and manufacturing tolerances.
Grid division
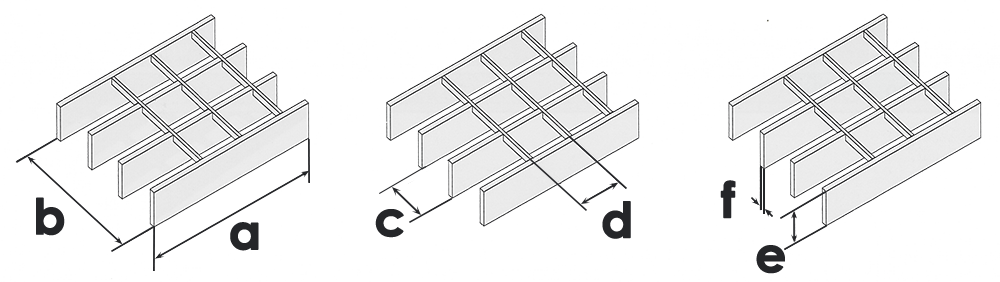
a = dimension of the sheet in the longitudinal direction of the bearing bars (support direction); b = dimension of the sheet in the longitudinal direction of the transverse bars; c = the division of the bearing bars; d = the division of the transverse bars; e = the height of the bearing bars; f = the thickness of the bearing bars
Grating types
Pressed gratings – P

The pressed gratings are used in all the industries to form different buildings, floor platforms, pavements, walking surfaces and landings.
Due to their outstanding qualities they are suitable for the high building regulations as well. The wide range of the possible dimensions and formations make possible lots of usages. In case of loading by vehicles it is advised to incorporate gratings with high load supporting capacity, while in case of presence of oily liquids, or snow and ice, to use anti-slip shaped grids. The pressed grids with dense division are used in public spaces, in front of the entrances of the buildings and in other such sites where the use of the basic gratings is not possible. Besides their usage in the industrial and building industry sectors, the pressed walking grids can be used very well as facade grids, shadings, escape routes, covering grids, and as the covers for the gas heating convectors.
Structure
The unweakened transverse bars are pressed with high pressure into the bearing bars which were previously cut to wedge shape. For this production process a press with a pressing force of 20.000 kN is used. The high pressure and the shape of the cuttings of the holding ribs guarantee a grating structure which is strong and has high convolution rigidity. The distribution of the loading is favourable. This is why the cuts, which may occur as a necessity later during the building operation influence very little the structural rigidity of the structure of the gratings.
Manufacturing dimensions
The pressed gratings are manufactured according to the dimensions and strength demanded by the market, always at the given dimensions. In the transverse direction the manufacturing dimension cannot exceed 1400 mm.
Framing
The pressed gratings made with a bearing bar of 20 x 2 mm to 40 x 3 mm are basically manufactured with T hemming, but U hemming or framing with flat strip may be ordered as well. The pressed gratings with a bearing bar over 40 x 3 mm are framed with flat strips.
Protection against corrosion
The finished welded gratings are hot dip galvanized.
Standard programme
The flexibility of the manufacturing equipment makes it possible to produce the most different types of gratings. Within the divisions it is evident that the rectangular grid division may also be chosen. There is the possibility of change within the basic division as well, e.g. the bearing bar division is 22.22 mm, the transverse bar division is 33.33 mm.
It has to be taken into account that at the surfaces to be loaded with vehicles the maximum grid division according to the regulations cannot exceed 33 x 50 mm.
The thickness of the transverse bar at the 2 mm thickness of the bearing bar is again 2 mm. Otherwise the transverse bars are 1-2 mm weaker than the bearing bars.
The transverse bars are 10 or 20 mm high depending on the height of the bearing bars.
Type designation
From the type mark of the pressed gratings the manufacturing mode is deducted (pressed), the bearing bar, the grid division and the framing. The anti-slip gratings are marked with an X before the type marking (e.g. XP 330-33-3).
Example:
P 330-33/44-3
P: pressed grating
330: bearing bar ø 30×3 mm
33: bearing bar grid division 33.33 mm
44: transverse bar grid division 44.44 mm
3: frame ø 30×3 mm
In case of the same bearing and transverse bar grid division the grid division is given only once e.g. : P 330-33-3
Individual manufacturing
The pressed gratings as building elements are linked to the manufacturing programme in different shapes and finishes. These may be for example shading elements, spoilers, dividing elements, decorative elements and many others. The grids may be manufactured with 45° and 15° oblique transverse bars.
Complete sieves
We offer so called complete sieves as decoration element, for example, suspended ceiling, railing element, shading, that is such pressed grids at which the dimensions of the supporting grid and the side grid are the same. the complete grids are manufactured up to the material thickness of 3 mm and to the maximum building height of 60 mm.
The types of the pressed gratings
Ultra finish: the surface of the bearing and the transverse bars is smooth.
GS-finish: the bearing bars, or the transverse bars, or all the bars are saw-toothed for the anti-slip finish.
GS1: saw-toothed transverse bars
GS2: saw-toothed bearing bars
GS3: saw-toothed bearing and transverse bars
The transverse bars do not take part in supporting the load, they only join and strengthen the bearing bars against turning outwards.
Welded gratings – SP

The welded gratings may be used at the industrial buildings as floor platforms, landings and floor elements for walking surfaces. The grids with greater load resistance are used in case of greater weighs arising from traffic. The anti-slip products are to used at sites which are polluted with oil and other oily materials.
Structure
The twisted or round transverse bars are pressed with high pressure into the unweakened bearing bars within a working corridor and at the same time they are welded using resistance welding procedure.
Resistance
During the resistance welding procedure all the cross points are homogeneous, and due to the solid welding they are outstandingly solid, with the greatest possible resistance thus forming an optimal load-spreading grating.
Ability of cutting
The special structural characteristics of the welded gratings make them outstandingly rigid against twisting and to be cut. Even at the later cuts which are usually unavoidable when mounting, the converging strength and the rigidity of the gratings remains untouched in a high proportion.
Framing
The hemming of the welded gratings stands of steel strips both in the direction of the bearing and of that of the transverse bars. The frame is made of strips at the high load-bearing gratigns as well.
Protection against corrosion
The finished welded gratings are hot dip galvanized.
Security
The bearing bars welded onto the upper side of the gratings give stable grip for the feet so this contributes to the increase of the security and to minimizing the workplace accidents.
Manufacturing width
According to the manufacturing process of the welded gratings always the standard 1000 mm (in the direction of the transverse ribs) carpet (Matte) is manufactured. Due to the shrinking following the welding the effective width is cca 998 mm, which has to be taken into account when placing the grid. Besides the 1000 mm standard width, smaller special dimension can also be manufactured.
Type designation
From the type marking of the welded gratings their manufacturing mode (welded), the bearing bar, the grid division and the framing can be determined. The anti-slip walking grids are marked with an X before the type marking (e.g. XSP 330-34/38-3).
For example: SP 330-34/38-3
SP: welded grating
330: bearing bar ø 30×3 mm
34/38: grid division 34×38 mm
3: frame ø 30×3 mm
Other technical terms regarding the gratings
Division picture
In all the tables the first dimension shows the distance between the main ribs, the second the distance between the side ribs.
Bearing bars
Transverse bars
The meeting points are pressed into each other, and in some cases they are strengthened by welding.
Seat
The seat has to be equal with the height of the bearing bars but cannot be less than 30 mm.
Ankle lath
Lowered hemming
Cuttings
The cutting below 0.5 metres is considered small figure cutting.
Hemming
Angular steel strip hemming
The length of the angular steel strip has to be at least equal with that of the bearing bar.
Back pinch
On stock
types | dimension of the sheet (mm) | quality of the material | Webshop |
SP 230-34-38-3 | 500 x 1000 | galvanised steel | BUY NOW |
SP 230-34-38-3 | 600 x 1000 | galvanised steel | BUY NOW |
SP 230-34-38-3 | 800 x 1000 | galvanised steel | BUY NOW |
SP 230-34-38-3 | 900 x 1000 | galvanised steel | BUY NOW |
SP 230-34-38-3 | 1000 x 1000 | galvanised steel | BUY NOW |
SP 330-34-38-3 | 1000 x 1000 | galvanised steel | BUY NOW |
SP 330-34-38-3 | 1200 x 1000 | galvanised steel | BUY NOW |
Stair elements out of gratings
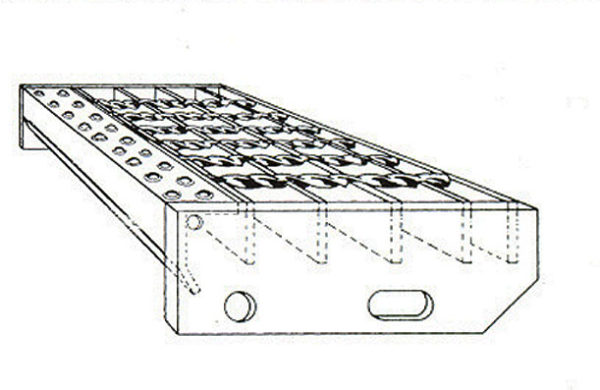
Structure
The steps of the stairs are made from the same type of grids as the pressed (P) or the welded (SP) gratings. These are always delivered with anti-slip, perforated entry edge and welded side plate. Each step is made using protective gas welding so the slag forming can be avoided together with the deformation of the step. The steps manufactured this way have precise angles and dimensions.
Mounting
Since the stairs can be manufactured according to the DIN standard with negative tolerances and the stair structures are also characterized by these tolerances, it is necessary to check before bolting the stairs whether a shim is needed between the stair support structure and the stair. This prevents damage to the support ribs' welds on the side plate.
Shaping of the longitudinal orifice
During the mounting in order to get easier positioning of the stair structure, the stairs are always made with a circular and a longitudinal orifice.
The perforated entry edge increases the static value of the stair and shows in an optically favourable manner its first edge. This contributes importantly to the security.
If needed we deliver fixing elements for the stairs which comprise of the following:
– hexagonal screw M 12 x 35 ISO 4016 (DIN 601)
– hexagonal headed nut M 12 ISO 4032 (DIN 934) és
– washer A 14 DIN 7989
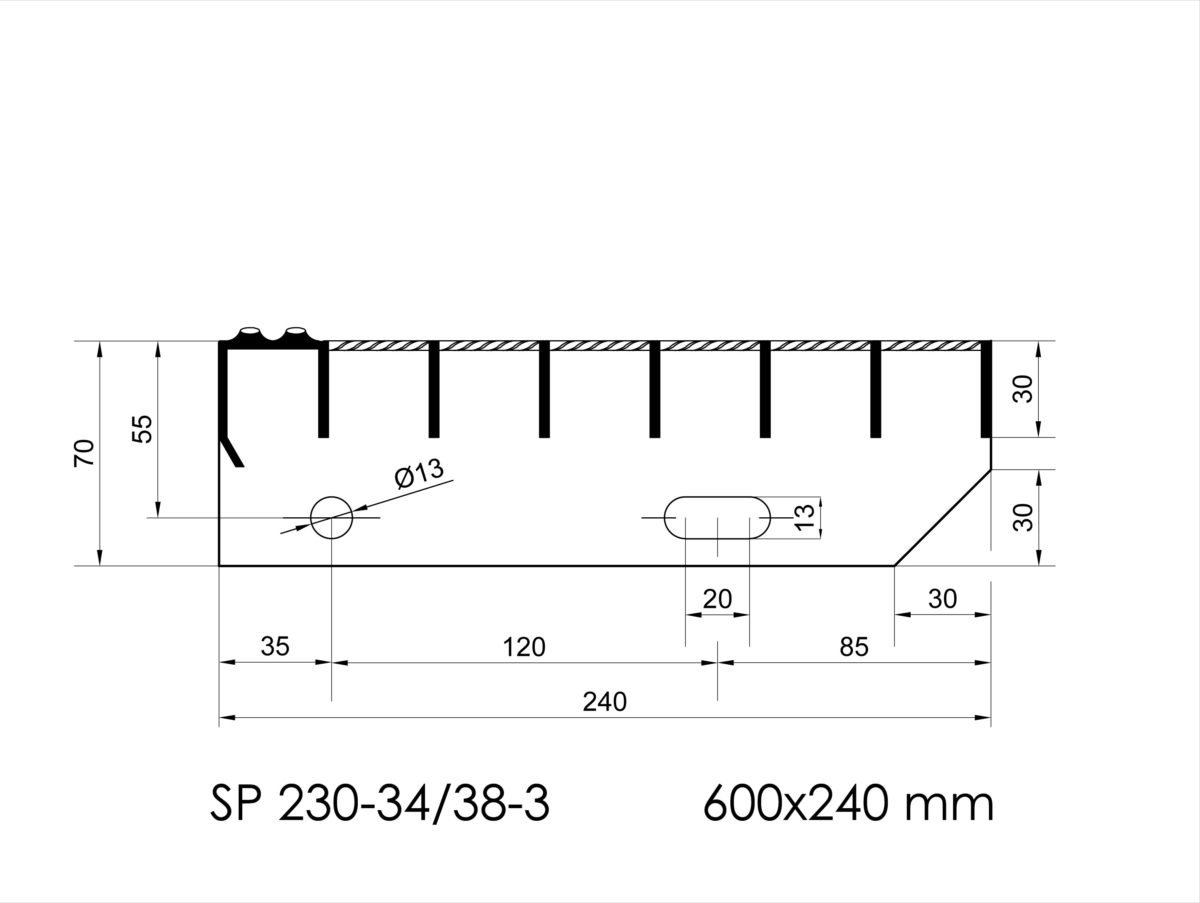
On stock
types | dimension (mm) | quality of the material | Webshop |
SP 230-34-38-3 | 600 x 240 | galvanised steel | BUY NOW |
SP 230-34-38-3 | 800 x 270 | galvanised steel | BUY NOW |
SP 330-34-38-3 | 900 x 270 | galvanised steel | BUY NOW |
SP 330-34-38-3 | 1000 x 270 | galvanised steel | BUY NOW |
SP 340-34-38-3 | 1200 x 270 | galvanised steel | BUY NOW |